The plywood production process is a decisive factor in the quality of the product when it reaches consumers. As a versatile material, plywood is widely used in the wood industry, from furniture to construction. To create high-standard plywood, understanding and controlling the production process is extremely important for manufacturers, businesses and consumers.
In this article, GREEN MECH will explore with you the role of wood chips in plywood panel production. We will provide a detailed look at the production process, helping you better understand the steps and applications of wood chips, ensuring the quality and effectiveness of plywood products on the market.
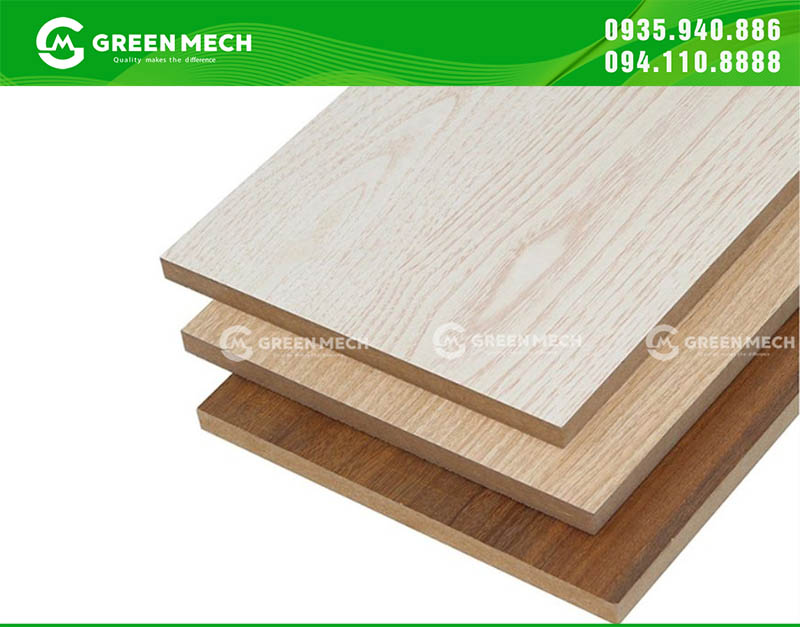
MỤC LỤC
The importance of plywood production process
Product quality assurance
Careful selection and processing of raw materials is the first step to ensuring plywood quality. Good raw materials, through processing steps such as peeling and cutting into chips, will create a final product with high durability and aesthetics.
The pressing and pressing techniques determine the adhesion and connection between the plywood layers. This process must ensure that the glue is evenly distributed and that the compression pressure is strong enough to create a strong board.
Surface machining helps create boards with smooth and uniform surfaces. Final quality inspection ensures that the product is free of defects and meets standards for thickness, durability, and aesthetics.
Enhance production efficiency
Modern production processes help optimize production stages, minimizing waste of materials and time. This not only reduces production costs but also improves the efficiency of the production line.
Applying advanced technology in stages such as heat pressing, automatic cutting and quality control helps ensure high accuracy and efficiency, thereby improving productivity and minimizing product errors.
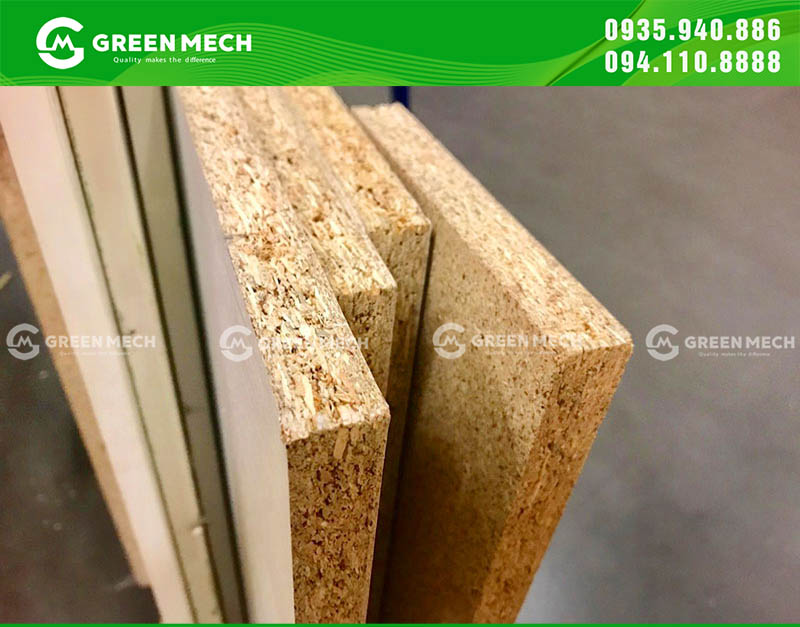
Protect the environment and resources
The efficient plywood production process helps make the most of wood resources, from waste wood to small pieces of wood, contributing to reducing pressure on exploitation of primary forests.
The waste treatment and recycling steps in the process help reduce the amount of waste generated, contributing to environmental protection and minimizing negative impacts on the ecosystem.
Meet diverse needs
Plywood produced according to standard processes can be used in many fields, from construction, furniture, to shipbuilding and packaging. This helps meet the diverse needs of the market with quality and sustainable products.
The production process can be adjusted to produce plywood with different properties, meeting the specific requirements of each application, from thickness and size to water resistance and load-bearing properties.
Types of machines used in plywood production lines
- Wood sawing machine: This machine is used to cut logs into wooden panels with a certain thickness and width to prepare for the next production process.
- Wood mill: This machine is used to grind wood into powder form, reducing moisture and introducing it into the manufacturing process.
- Presses: Presses use pressure and temperature to press wood and glue together to form plywood panels.
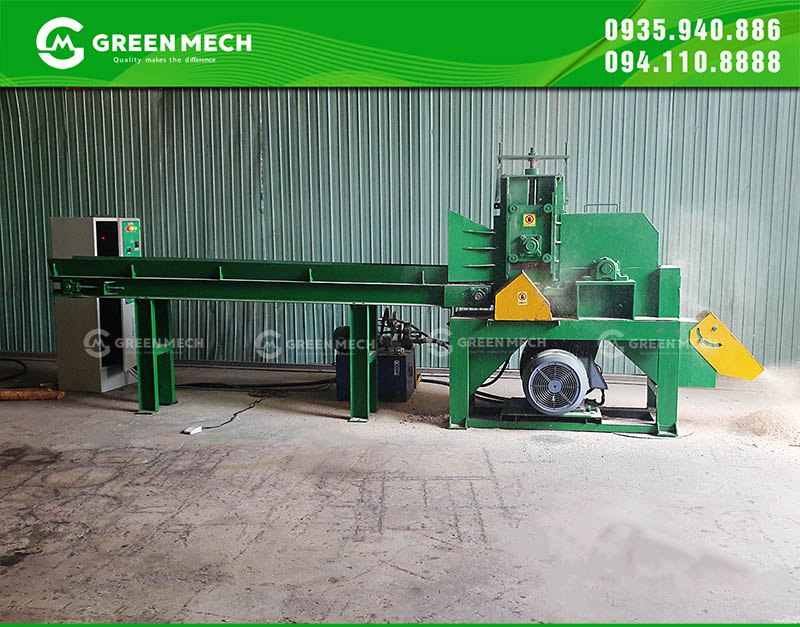
- Sander: This machine is used to sand the surface of the plywood panel to achieve the desired smoothness and shine.
- Profile saw: This machine is used to cut plywood panels into different shapes to meet customer requirements.
- Edge banding machine: This machine is used to edge plywood to form larger sized plywood panels.
- Surface smoothing machine: This machine is used to smooth and polish the surface of plywood panels to achieve a smoother and more beautiful surface.
What are the raw materials used in the plywood production process?
The main materials used in the plywood production process include Sawdust crusher and glue. Commonly used woods are hardwoods such as acacia, pine, red star, ash, acacia and other woods. Wooden panels are cut into boards from 1 to 6 mm thick.
Pressed glue is a type of glue produced from wood particles such as glue, rubber or melamine. This glue is mixed with other chemicals to create an adhesive that is heat-resistant and water-resistant. The wooden panels are then coated with a layer of adhesive before being pressed together at high temperature and pressure to form plywood panels.
In addition, during the plywood production process, other additives such as colorants, odorants, durability agents, viscosity agents, etc. are used to increase the properties and quality of the final product.
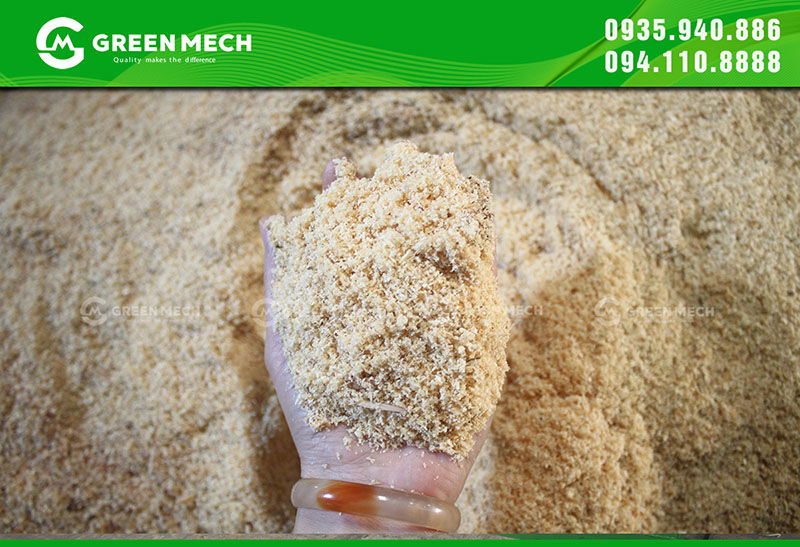
Outstanding features of GREEN MECH sawdust wood crusher
- GREEN MECH wood crushing equipment can crush a variety of materials, including trees, slats, cardboard, and dominoes.
- The machine is equipped with an automatic sawdust feeding and output system, minimizing labor and operation costs.
- GREEN MECH uses hydraulic technology to save up to 70% on energy costs compared to old technologies.
- The machine can be controlled automatically or manually with a stable hydraulic motor and a grinding knife life of up to 1000 hours.
- GREEN MECH is considered the leading technology in Vietnam in grinding wood into sawdust.
Contact to buy a machine that crushes wood into sawdust
We would like to sincerely thank our readers for taking the time to read this article about industrial wood crushers at GREEN MECH.
We hope this article has provided enough information and helped customers better understand the product as well as why they should choose to buy a wood crusher at GREEN MECH.
In particular, we look forward to cooperating and providing quality products to customers. With experience and professionalism, we are committed to providing the best products, reasonable prices and the best after-sales service.
GREEN MECH Vietnam specializes in manufacturing and supplying sawdust crusher from small scale to export. Any need for advice on investment in wood chipper machine, please visit the website: https://biomass.vn/ or contact Hotline (Zalo): +84 935.995.035 or call center: +84 941.108.8888 or leave information in the form, we will contact you right away.
Once again, we sincerely thank you for your interest in our products. Wishing our customers good health and success in work!